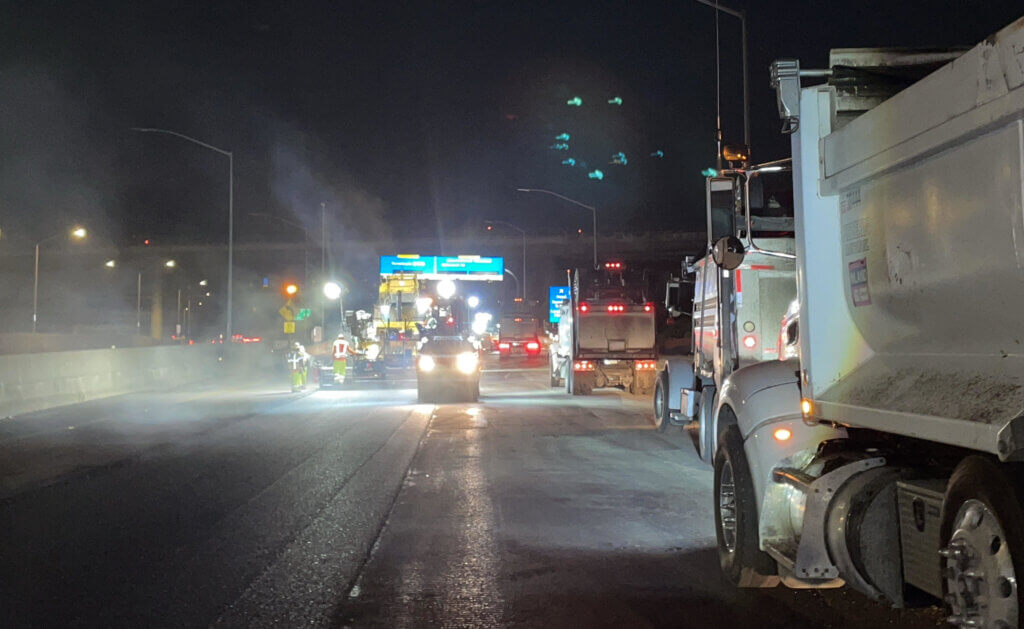
Project Description
San Mateo County
The Highway 101 On/Off-Ramp Rehabilitation Project stands as a powerful example of formal construction partnering in action. Spanning from 101/Oyster Point Blvd to 101/Millbrae Ave along the primary arterial route to San Francisco International Airport (SFO), this high-profile project required seamless coordination to maintain uninterrupted airport service, minimize delays, and ensure the highest level of safety for the traveling public.
Delivered through a tightly coordinated effort between San Francisco International Airport (SFO), Bay Cities Paving and Grading, and Caltrans, the project rehabilitated critical ramp infrastructure including 41 concrete barrier transitions—over 80% of which were impacted by underground utility conflicts. Aimed at improving safety and operational efficiency, the work entailed widening loop connectors, eliminating merge conflicts, realigning exits, and incorporating Complete Streets and Active Transportation elements like a new bikeway and enhanced pedestrian access. The team navigated night shifts, scheduling complexities, and strict environmental regulations, including protections for endangered species and stormwater controls. Despite these challenges, the project was completed on time, under budget, and with minimal disruption—all while upholding high standards of safety and quality.
Partnering in Action
From the outset, formal Construction Partnering, facilitated by VELO Group, unified the project stakeholders around a common set of stretch goals related to safety, schedule, quality, budget, public convenience and environmental stewardship.
These goals were developed collaboratively during the initial Partnering Kick-Off Session and evaluated regularly through team surveys and milestone reviews. The team also completed Partnering Skills Development Training, including lessons on process goals, issue resolution and risk assessment.
Key Partnering Contributions to Success
- Innovative RFI Resolution Process:
Night crews submitted photos of issues directly to the Project Manager and Resident Engineer. This proactive communication loop allowed concerns to be discussed and addressed in real time, often before the next work shift began—minimizing delays and streamlining documentation. - Conflict Resolution Strategy:
While a Dispute Review Board (DRB) was established per contract, no disputes escalated to a hearing. All issues were resolved at lower levels through the Issue Resolution Ladder, showcasing the strength of the team’s collaborative culture. - Adaptive Traffic Control:
Recognizing the importance of public convenience and safety, the team jointly developed a change order to substitute selective lane closures for full ramp closures. This adjustment included portable message signs and attenuator trucks, allowing for safer, more flexible construction while reducing the impact on the traveling public. - Seasonal Schedule Optimization:
Through mutual agreement, the project’s start was deferred from December 2022 to April 2023, avoiding the wet season. This decision mitigated environmental risks (e.g. endangered species: garden snake and red legged frog) and improved operational efficiency during peak construction. - Shared Resource Coordination:
Another contractor working within the same project limits collaborated on shared lane closures, reducing public impact and avoiding scheduling conflicts—yet another benefit of the cooperative partnering environment.
Partnering in Practice: Driving Unity and Results
Throughout the project, weekly meetings, virtual collaboration tools, and pre-shift coordination sessions between field inspectors and foremen maintained transparency and momentum. Each formal partnering session included working lunches and team-building activities, reinforcing interpersonal connections and fostering a “one team” mindset. Further, relationships were often enhanced with the use of virtual meetings, fostering a proactive approach to problem solving.
The 101 Ramp Rehabilitation Project proves that Construction Partnering isn’t just a process—it’s a performance multiplier. By uniting diverse organizations under shared goals, the team delivered exceptional results for the community, stakeholders and the traveling public.
Partnering Results
- Estimated Partnering ROI : $366,998 / $20.46 saved per dollar spent
- Completed on schedule and under budget
- High team survey ratings
- Enhanced stakeholder communication and alignment
- Streamlined issue resolution
- Fostered high quality construction
- Met worker and public safety goals
- Mitigated public impacts
- Zero environmental violations
Project Notes
- Cost: $18,243,709.33
- Schedule: 210 Days
- Labor hours: 40,645
- Project Stakeholders: 9
- Partnering Sessions: 2
Awards
2025 Caltrans Excellence in Partnering Award