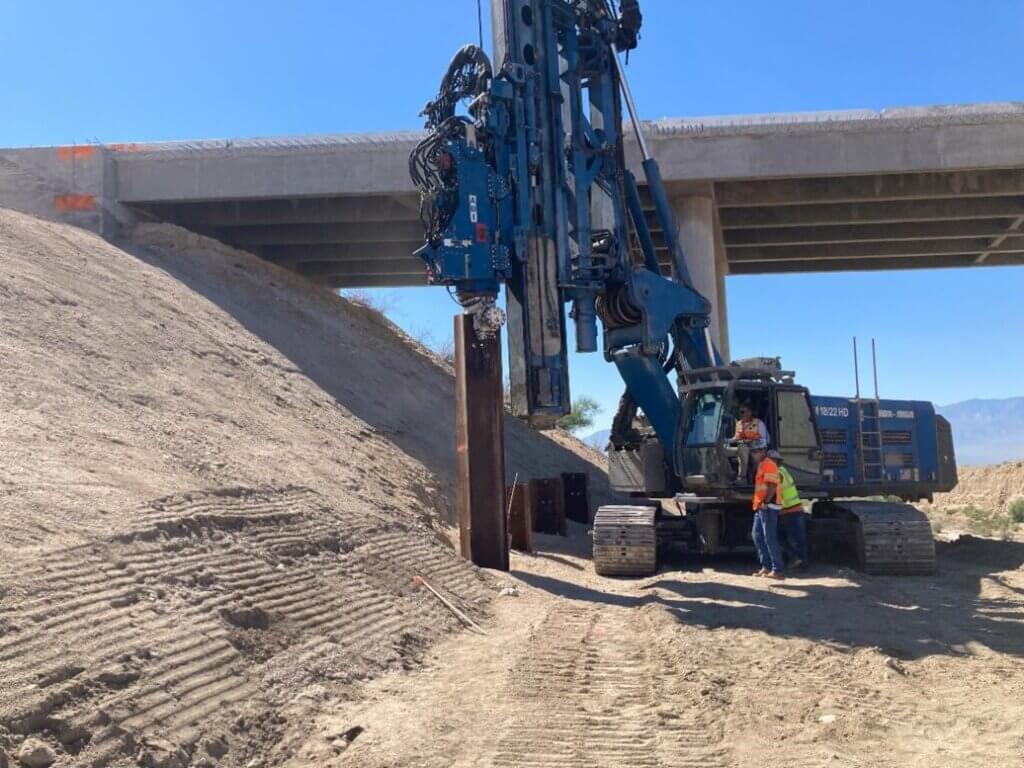
Project Description
Desert Center and Blythe, California
Located in the remote low desert between Desert Center and Blythe, California, this highway project involved rehabilitating a 30-mile stretch of East and West Bound Interstate 10 by removing existing Hot Mix Asphalt (HMA) and replacing it with Jointed Plain Concrete Pavement (JPCP). The scope also included modifications to 46 bridges, installation of Placed Rock Slope Protection (PGRSP) at 22 ditch locations, and the creation of median clear recovery zones to enhance safety and improve drainage.
Partnering Approach
The project team embraced a comprehensive Construction Partnering framework from the start. This involved 10 professionally facilitated partnering workshops, including a kickoff and a closeout session. Team-building activities, conflict resolution training, collaborative decision-making, and win-win negotiation sessions were core components of the process.
A Dispute Resolution Ladder (DRL) was developed during the kickoff session, giving all stakeholders a structured, agreed-upon process for resolving challenges. The team identified critical goals early on, regularly evaluated progress, and ensured that all parties were accountable. Further, monthly surveys conducted by partnering facilitators safeguarded ongoing alignment with project goals.
Overcoming Remote Site Challenges
Due to the project’s isolated location—far from urban centers, emergency services, and suppliers—several unique challenges arose.
Initial detour plans would have required extensive bridge and roadway widening. In response, the project’s contractor Fisher Sand & Gravel worked with Caltrans to develop and propose a Value Engineering Change Proposal (VECP), which allowed traffic to be staged along the median in both project phases. This eliminated the need for the originally planned widening, reduced costs significantly, minimized disruption to the traveling public, and improved overall corridor safety.
The revised plan also allowed changes to the roadway profile, removing overtopping concerns and delivering a more uniform pavement section. The team worked closely with district and headquarters staff to ensure environmental compliance and address regulatory concerns without compromising on quality or schedule.
Innovation and Quality Through Collaboration
In addition to implementing the VECP, the team introduced several key innovations, including the first use of pre-cast approach slabs on bridge retrofits, Hot Mix Asphalt with 40% Reclaimed Asphalt Pavement (RAP), and FHWA-approved stitching to repair cracks in JPCP.
A shared quality goal—limiting rejected concrete to under 1%—united the contractor and owner teams. Support from the Southwest Concrete Pavement Association helped establish best practices that resulted in some of the smoothest, highest-quality pavement in the district.
When unexpected cracking occurred, the team did not assign blame but instead collaborated on a solution with outside experts to implement targeted FHWA-approved repairs, preserving both schedule and budget while introducing a valuable repair method for future use.
Engaging the Entire Team
The partnering process extended beyond management to include all field and craft personnel. Goals were clearly communicated to contractor staff and subcontractors, with milestone-based incentives—like BBQs—boosting morale and reinforcing teamwork.
Due to the remote location, team-building activities such as dinners and river outings helped strengthen bonds and support staff retention. Subcontractors were actively involved from the start, contributing to goal-setting and participating in issue resolution discussions. This inclusive approach fostered collaboration, accountability, and efficient problem-solving throughout the project.
Effective Issue Resolution
One of the first major tests of the DRL came during negotiations around the VECP. While all parties agreed on the proposal’s merits, they could not initially reach consensus on the cost savings. The DRL allowed the issue to be escalated constructively to the executive level, where a mutually agreeable solution was reached. This preserved working relationships and allowed the project team to focus on execution rather than conflict.
By the time the Proposed Final Estimate and Contract Acceptance were reached, the project had no outstanding claims—proof of the effectiveness of the partnering process.
Partnering Results
- Estimated ROI: $8.73 million / $165 saved per dollar spent
- Completed on schedule
- $3.8 Million under budget
- No outstanding claims
- Enhanced communication and decision-making
- Innovative solutions implemented
- High quality construction
- Minimized public and environmental impacts
Project Notes
- Schedule: 765 Days
- Contract Value: $264 Million
- Labor Hours: 105,036
- Facilitated Partnering Sessions: 10
Awards
- 2025 Caltrans Excellence in Partnering Award
- 2023 Emergency Response/ Repair Project of the Year by the California Transportation Foundation