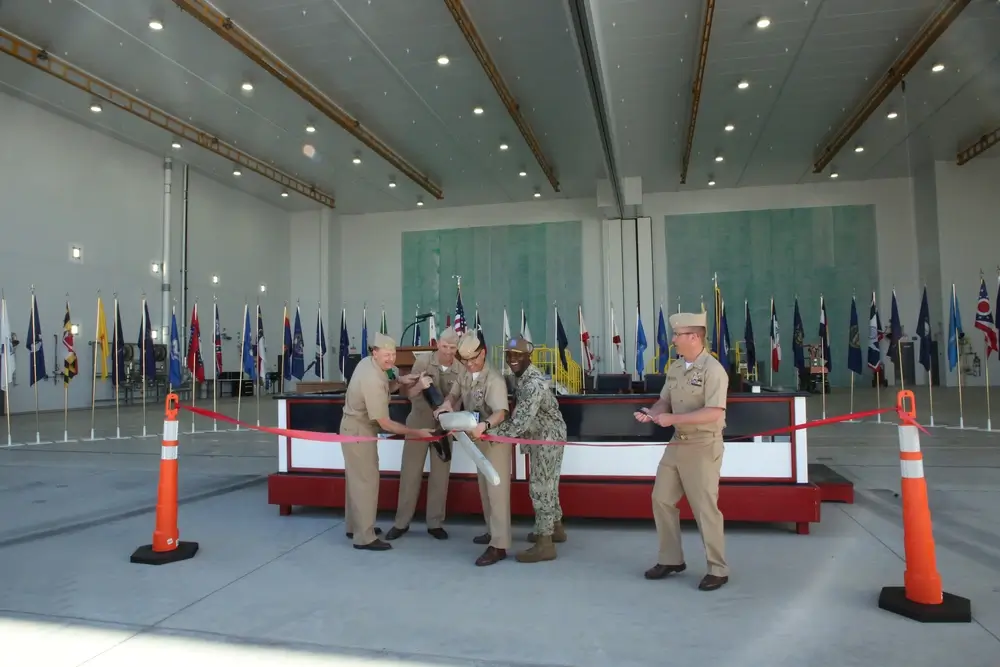
Project Description
San Diego, CA
Completion of the Fleet Readiness Center Southwest’s (FRCSW) Aircraft Paint Complex at Naval Base Coronado stands as a pivotal achievement in the Navy’s ongoing commitment to manage a growing workload to accomodate the fleet’s demands. The new paint complex was designed to accommodate a diverse range of military aircraft vital to operational effectiveness enabling safe and secure maintenance for fourth-generation aircraft while also preparing for the integration of fifth and sixth-generation planes. With a strong emphasis on ensuring the safety and efficiency of personnel, the complex is poised to seamlessly support daily operations.
Built on an active Naval Base, the project involved construction of a dedicated 51,785-square-foot facility for paint and corrosion control, incorporating four paint bays, a corrosion control bay, and a media blast bay equipped with cutting-edge technology. Two of these bays house fully automated partition walls, enabling the division of space for painting smaller aircraft. The building also includes a wash rack, facilitating aircraft cleaning by crew members prior to their entry into the maintenance facility.
Additional amenities comprise strategically partitioned outer entry halls designed for support spaces with air-pass-thru-showers, a secured exterior roof access stairway leading to interior catwalks and roof maintenance areas, and centrally positioned utilities that reduce run distances.
At the outset, facilitated project partnering was employed to unify team members towards the shared objectives of the project. In the inaugural partnering session, the team established mutual goals encompassing schedule adherence, safety protocols, operational efficiency, budgetary constraints, quality standards, collaborative teamwork, and decision-making processes. Additionally, they established communication strategies and procedures for resolving issues. These objectives were periodically reviewed, assessed, and modified when necessary, during the project’s progression.
The pandemic brought further challenges successfully mitigated through a collaborative mindset and the partnering tactics already in place. Completed on schedule and within budget, the facility stands as a testament to the project team’s exceptional partnership.
Partnering Results
- Completed on schedule and within budget
- Enhanced communication
- Efficient QC/QA Process
- Increased sharing – learning from others
- Facilitated real-time problem solving
- Mitigated interruptions to existing operations
- Minimized RFI’s
- Facilitated timely and efficient equipment delivery
- Zero OSHA Recordable Safety Incidents
- Mitigated challenges
- Heighten coordination and teamwork
Project Notes
- 51,785 square feet
- $74 Million