Project info
- Case Studies
U.S. Department of Veterans Affairs
Cambridge Healthcare Solutions
Mascaro Construction
Stantec
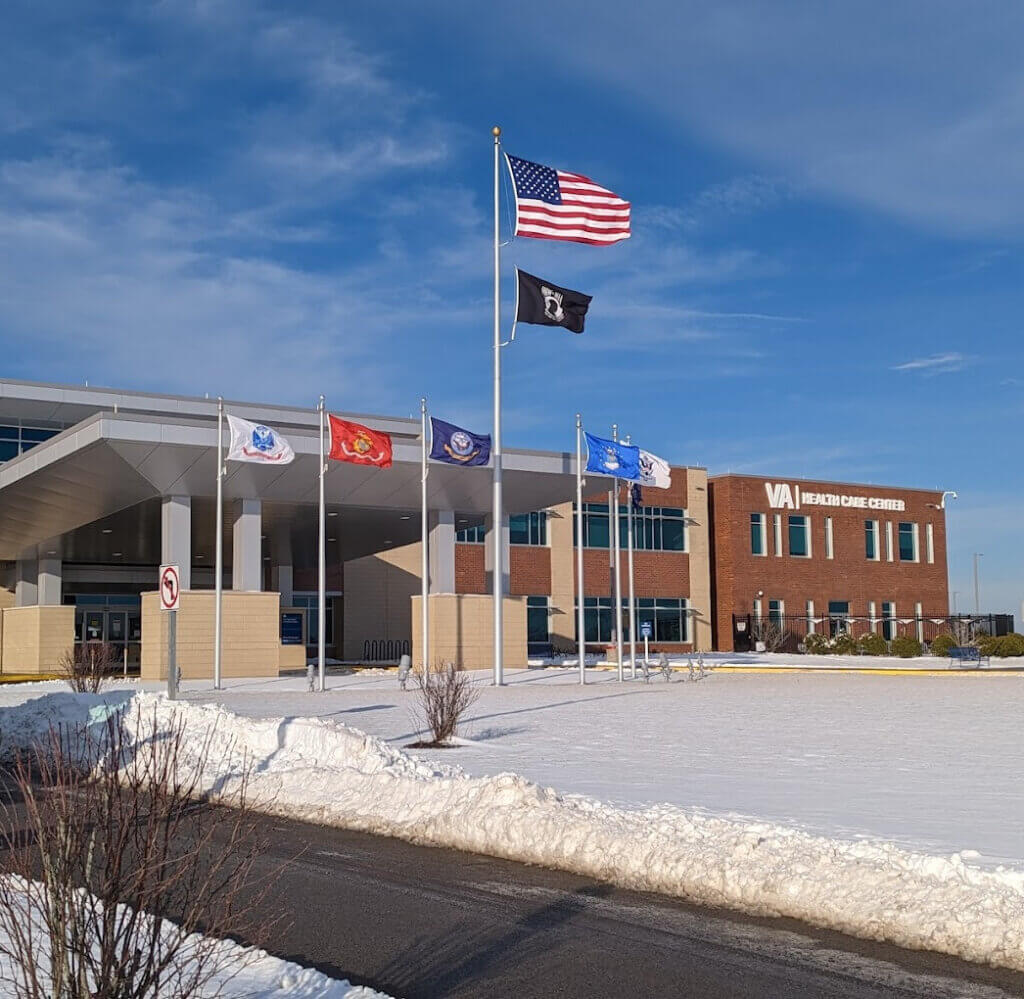
Project Description
Butler, Pennsylvania
The Abie Abraham VA Clinic, located in Butler, Pennsylvania, stands as a testament to effective collaboration in healthcare infrastructure development. This state-of-the-art healthcare center was designed to enhance outpatient services for nearly 20,000 veterans across western Pennsylvania.
The project encompassed a 251,000-square-foot, two-story building, and more than 1,300 parking spaces. The new facility integrates a variety of healthcare services from primary care to specialty care, mental health, dental, diagnostic, laboratory, pathology, radiology, podiatry, optometry, pharmacy, physical rehabilitation, and women’s health. Its design, featuring nine Patient Aligned Care Team (PACT) areas with individual waiting rooms and LEED Silver certification, reflects both local heritage and modern healthcare needs.
In addition to facing challenges typical of large-scale healthcare construction, the project encountered stringent budget constraints, adherence to VA standards, extensive public outreach and a demanding timeline. Moreover, coordinating diverse stakeholders—from governmental agencies to healthcare providers—was crucial to ensure seamless project execution. These challenges necessitated a robust partnership approach to navigate complexities and deliver results efficiently.
Facilitated by a public-private partnership (P3) between Cambridge Healthcare Solutions PA, Stantec, and Mascaro Construction Company, the VA Clinic project employed a structured partnering strategy. This approach fostered a collaborative environment from the project’s inception, ensuring alignment on goals related to the facility, veterans’ experience, schedule, safety, public relations, quality, budget, employee experience, and teamwork. When goals were not being met, the team assessed new information and tasks, developed revised plans, and adjusted smaller objectives to achieve the larger ones.
Five partnering sessions over 15 months along with monthly meetings and weekly calls fostered proactive issue resolution, maintained communication channels, and upheld project momentum. Frequent meetings of the entire team allowed real time discussion and immediate development of solutions. In each meeting, the team worked together through outstanding issues related to project goals. This gave all attendees opportunities to improve upon the plans and the work, leading to an improved schedule, budget and quality construction.
The partnership also prioritized innovation, such as integrating sustainable building practices and optimizing operational efficiencies. Despite changes in project scope, the team completed the project months ahead of schedule without additional costs. The project concluded with social gatherings and public events, including topping out and ribbon-cutting ceremonies, where veterans and community members celebrated the facility’s expansion.
Partnering Results
- Early Completion: Completed over eight months ahead of schedule, demonstrating the efficiency and synergy of the partnering approach.
- Cost Efficiency: Vigilant cost management by the team resulted in the project completing $123.8 million under budget.
- Project Savings: $3,120,000 in estimated savings attributed to partnering.
- Enhanced Quality: Maintained high standards of construction quality and design integrity.
- Safety: Zero lost work hours to workplace safety issues.
- Sustainability: Implemented LEED Silver standards.
- Community Engagement: Positive public sentiment and media coverage.
Project Notes
- Project Cost: $66.2 Million
- Project Size: 251,000 square feet
- Construction Duration: 433 work days
- Work hours: 285,000
- Delivery Method: Public Private Partnership (P3) & Construction Manager at Risk (CMAR)
- Certification: USGBC LEED Silver Certified